steel mill crane Safety Certifications
Steel mill cranes are essential for handling heavy materials and equipment within the mill. Ensuring their safe operation is crucial, which is why several certifications and standards exist to guide their design, installation, and use.
1. OSHA (Occupational Safety and Health Administration): OSHA standards set forth the requirements for crane operation safety in the United States. Compliance ensures adherence to regulations on equipment maintenance, operator training, and safety protocols.
2. ANSI (American National Standards Institute)/ASME (American Society of Mechanical Engineers) B30: This standard covers the safety requirements for various types of cranes, including those used in steel mills. It includes guidelines for construction, installation, maintenance, inspection, and operation.
3. ISO (International Organization for Standardization) 9001: This certification pertains to quality management systems and ensures that the crane manufacturing process adheres to globally recognized quality standards.
4. CMAA (Crane Manufacturers Association of America) Specification No. 70: This specifies the design and manufacturing criteria for electric overhead traveling cranes, commonly used in steel mills. Adherence to CMAA standards ensures robust, reliable, and safe crane operations.
5. EN (European Norm) 15011: Relevant for cranes operating in European steel mills, this standard addresses requirements for the design, manufacturing, testing, and operation of cranes.
6. IEC (International Electrotechnical Commission) Standards: IEC standards, particularly IEC 60204-32, outline the safety aspects relating to the electrical equipment of cranes.
7. FEM (Federation Europeenne de la Manutention) Standards: These provide guidelines on the mechanical aspects and load handling attachments for cranes.
—
Ensuring compliance with these certifications and standards helps steel mill operators maintain high safety levels, reduce operational risks, and protect their workforce from potential hazards.
List Reference Technical Parameters of “steel mill crane”
Sure, here are the key technical parameters of a steel mill crane:
1. Load Capacity: Defines the maximum weight the crane can lift. Steel mill cranes typically have high load capacities ranging from 15 to 500 tons or more depending on the application.
2. Span: The horizontal distance between the rails or tracks on which the crane travels. Typical spans range from 10 to 35 meters.
3. Lifting Height: The vertical distance the hook can travel. Heights usually range from 10 to 30 meters, based on the requirements of the mill.
4. Crane Speed: Includes hoisting speed, trolley travel speed, and crane travel speed. These speeds vary, but typical values are:
– Hoisting Speed: 1 to 20 meters per minute.
– Trolley Speed: 10 to 60 meters per minute.
– Crane Travel Speed: 20 to 120 meters per minute.
5. Duty Cycle/Class: Indicates the crane’s operational uptime and stress level. Standard classifications are A6 to A8 (FEM) or Class D to E (CMAA), signifying medium to heavy-duty usage.
6. Control System: Can be radio remote control, cabin control, or pendant control. Modern steel mill cranes often use advanced automated control systems for precision and safety.
7. Power Supply System: Generally includes cable reels, busbars, or festoon systems. Voltage levels typically range from 380V to 480V AC.
8. Temperature Range: Cranes in steel mills must withstand high ambient temperatures, often designed to operate from -10°C to 60°C or higher.
9. Motor and Drive Systems: Utilizes electric motors for hoisting and traveling. Inverter drives or variable frequency drives (VFDs) are commonly used for smooth operation and energy efficiency.
10. Safety Features: Equipped with overload protection, emergency stop systems, thermal protection for motors, and anti-collision devices.
11. Materials and Coating: Designed to withstand harsh environments, often using high-strength, corrosion-resistant materials with specialized coatings for longevity.
These parameters collectively ensure that steel mill cranes are robust, reliable, and capable of handling the demanding conditions typical of steel production environments.
List Product features of “steel mill crane”
Product Features of Steel Mill Cranes
1. High Load Capacity: Designed to handle extremely heavy loads typical in steel mills, ranging from several tons to hundreds of tons.
2. Robust Construction: Built with high-grade steel to withstand rigorous operational conditions and to enhance durability and longevity.
3. Heat Resistance: Equipped with materials and cooling systems that can withstand high temperatures prevalent in steel mills.
4. Precision Control: Advanced control mechanisms, including automation and computerized systems, ensure accurate load handling and placement.
5. Safety Features: Includes features such as overload protection, emergency stop buttons, and fail-safe mechanisms to ensure operator and equipment safety.
6. Versatility: Can be equipped with different attachments like electromagnetic lifters, hooks, and clamps, making them suitable for lifting various materials like ingots, slabs, coils, and billets.
7. Customizable Design: Tailored to meet specific operational needs, including different span lengths, lifting heights, and capacities.
8. Ease of Maintenance: Designed for easy access to critical components, reducing downtime and maintenance costs.
9. Energy Efficiency: Incorporates energy-saving technologies to reduce operational costs and environmental impact.
10. Operator Cabin: Ergonomically designed cabins with climate control for enhanced comfort and reduced operator fatigue, ensuring prolonged efficient operation.
11. High Stability: Features like anti-sway technology to ensure stable and smooth operation, minimizing the risk of load swing.
12. Advanced Monitoring: Incorporation of real-time monitoring systems for load, temperature, and mechanical stress to optimize performance and preventive maintenance.
13. Durable Motors: High-performance motors specifically designed for heavy-duty operations, ensuring reliable and consistent performance.
14. Smooth Operation: Utilizes frequency inverters and hydraulic systems for smooth acceleration and deceleration, enhancing operational control.
15. Environmental Adaptability: Can be adapted for use in extreme environmental conditions, such as high heat or highly corrosive atmospheres.
These features collectively ensure that steel mill cranes are highly efficient, reliable, and safe for the heavy-duty lifting tasks typically encountered in steel manufacturing and processing facilities.
List Various Types of “steel mill crane”
Steel mill cranes are specialized overhead cranes used in steel production and processing. Here are some common types:
1. Overhead Bridge Cranes:
– Single Girder Overhead Cranes: Usually lighter-duty, used for small to medium capacity lifting and material handling.
– Double Girder Overhead Cranes: Higher capacity, capable of handling heavier loads, and can travel longer spans.
2. Gantry Cranes:
– Full Gantry Cranes: Used for outdoor yards or areas without suitable runway structure, they run on ground tracks.
– Semi-Gantry Cranes: One side runs on ground level while the other side runs on an elevated runway.
3. Ladle Cranes:
– Specifically designed to handle liquid metal ladles during the smelting process. They are robust and come with specialized safety features to manage high-temperature materials.
4. Slab and Billet Handling Cranes:
– These cranes are configured to handle large pieces of steel such as slabs and billets, featuring specialized lifting attachments like magnets or clamps.
5. Charging Cranes:
– Used to feed raw materials into a furnace. These have high heat resistance and precision handling capabilities to place materials accurately.
6. Rolling Mill Cranes:
– Used to transport billets, slabs, or rolled products within a rolling mill. They are designed to withstand high temperatures and handle hot materials.
7. Manipulator Cranes:
– These are used for precise positioning of workpieces in various processes within steel mills. They often have robotic arms for detailed movements.
8. Maintenance Cranes:
– Deployed for the maintenance of mill machinery, they facilitate the regular upkeep and replacement of parts.
Each type of steel mill crane is designed to meet specific requirements of the operations, including lifting capacity, operational speeds, and environmental conditions like high temperatures and dust.
List Application of “steel mill crane”
A steel mill crane is a critical piece of equipment in metal processing and manufacturing industries. Here’s a list of its applications:
1. Material Handling: Steel mill cranes efficiently handle raw materials like iron ore, coal, and limestone, transporting them to different stages of the steelmaking process.
2. Hot Metal Handling: These cranes transport molten metal from the blast furnace to the basic oxygen furnace or electric arc furnace, ensuring continuous production.
3. Slab and Billet Handling: After casting, steel slabs, billets, and blooms are heavy and extremely hot. Steel mill cranes transport these items to rolling mills or storage areas.
4. Coil Handling: Finished steel coils, which can weigh several tons, are moved using specialized coil cranes to storage or loading areas.
5. Maintenance and Repairs: Cranes assist in the maintenance of heavy machinery and equipment within the steel plant by lifting heavy components during repair operations.
6. Loading and Unloading: They play a crucial role in the logistics chain, loading finished products onto trucks, trains, or ships and unloading raw materials arriving at the mill.
7. Waste Management: These cranes handle steel manufacturing by-products like slag and scrap, moving them to appropriate processing or disposal areas.
8. Batch Weighing: Certain cranes are equipped with weighing systems to measure and transport specified quantities of materials for production batches.
9. Safety and Efficiency: Reduce manual labor and enhance safety by managing heavy loads that are dangerous for human operators to handle.
10. Storage Management: Assist in the organized stacking and retrieval of materials in storage areas, optimizing space and inventory management.
Steel mill cranes are indispensable for the efficient, safe, and continuous operation of steel production facilities, ensuring smooth workflow and high productivity.
List Buyer Types of “steel mill crane”
Sure! Buyer types for steel mill cranes can vary significantly based on their specific needs and industry roles. Here are some common categories:
1. Steel Producers: Large steel manufacturing companies, often integrated producers, who require cranes for handling raw materials, semi-finished products, and finished steel products in their mills.
2. Construction Companies: Businesses involved in building or upgrading steel mills often need cranes for the assembly of heavy mill components and infrastructure.
3. Equipment Rentals: Companies that rent out heavy machinery, including steel mill cranes, to steel mills and construction firms.
4. Manufacturing Plants: Factories that produce steel-based machinery and equipment often require cranes for moving heavy parts.
5. Recyclers/Salvage Yards: Facilities that recover scrap steel for recycling may use cranes to handle large volumes of heavy materials.
6. Engineering and Procurement Services: Firms specializing in the design, procurement, and installation of industrial equipment, including cranes, for steel mills.
7. Distributors/Resellers: Entities that purchase cranes in bulk and resell them to smaller steel mills or other industrial operations.
8. Government/Public Sector: Includes national defense and infrastructure projects requiring heavy lifting equipment.
Each buyer type has unique requirements and priorities. For instance, steel producers prioritize reliability and capacity, while construction companies may focus on versatility and ease of assembly. Distributors look at cost-efficiency and resale value. Understanding these nuances is crucial for targeting the right buyer with tailored solutions.
In summary, the market for steel mill cranes includes varied buyers such as steel producers, construction firms, equipment rental companies, manufacturing plants, recyclers, engineering firms, distributors, and public sector projects. Each category has distinct needs that influence their purchasing decisions.
List “steel mill crane” Project Types for Different Industries
Steel mill cranes are vital in various industries, each tailoring crane types to meet specific needs. Here are the primary project types for different sectors:
1. Steel and Metal Production:
– Charging Cranes: Used for adding raw materials into furnaces.
– Ladle Cranes: Transport molten steel for casting.
– Billet and Slab Handling Cranes: Move heavy billets and slabs within the mill.
2. Construction:
– Tower Cranes: Erect tall buildings by lifting heavy materials like steel beams.
– Gantry Cranes: Provide heavy lifting capabilities on construction sites.
– Portable Cranes: Deliver flexibility for smaller or remote projects.
3. Automotive Industry:
– Jib Cranes: Assist in the assembly line, particularly in handling large components.
– Overhead Cranes: Used for moving molds and parts across production floors.
4. Shipbuilding:
– Goliath Cranes: Lift and transfer large ship sections.
– Floating Cranes: Operate in water to help assemble or repair ship parts.
– Dockside Cranes: Specifically for loading and unloading ship cargo.
5. Power Generation:
– Turbine Hall Cranes: Used for lifting and placing heavy turbine components.
– Transformer Handling Cranes: Specially designed for installing and maintaining large transformers.
6. Mining:
– Mine Shaft Hoisting Cranes: Elevate heavy loads from underground mines.
– Maintenance Cranes: Essential for the upkeep of mining equipment and vehicles.
7. Railway:
– Rail-Mounted Gantry Cranes (RMG): Used for handling large containers and cargo.
– Locomotive Maintenance Cranes: Used within facilities for maintaining trains.
Each industry requires cranes with specific features, capacities, and functionalities to meet their unique operational demands efficiently. Understanding these requirements ensures that the right type of crane is selected to optimize productivity and safety.
steel mill crane Accessories Upgrades and Custom Manufacturing Options
Upgrading and customizing steel mill crane accessories can significantly enhance operational efficiency, safety, and reliability. Here are key options to consider:
1. Hoist Upgrades: Modern hoists with variable frequency drives (VFDs) offer precise control and smoother operations, reducing wear and tear.
2. Load Monitoring Systems: Installing advanced load monitoring systems ensures accurate weight measurements, prevents overloading, and enhances safety.
3. Remote Controls: Wireless remote controls facilitate better maneuverability and safer operation by allowing operators to maintain a safe distance.
4. Smart Sensors: Integration of IoT sensors for real-time data on load, position, and equipment health can preemptively identify maintenance needs, minimizing downtime.
5. Anti-Sway Technology: Implementing anti-sway systems reduces the pendulum effect during load movement, improving operational precision and safety.
6. End Truck and Wheel Assemblies: Upgrading these components with high-quality, durable materials can extend the lifespan and reliability of the crane.
7. Trolley Systems: Custom trolleys for specific applications can optimize performance and meet unique operational needs.
8. Operator Cabins: Enhanced operator cabins equipped with ergonomic controls, better visibility, and climate control can improve operator efficiency and comfort.
9. Safety Features: Adding features such as emergency stop systems, collision avoidance sensors, and overload protection can significantly improve workplace safety.
10. Custom Fabrication: Tailoring components such as spreader beams, lifting magnets, and hooks to specific operational requirements can maximize efficiency and effectiveness.
Steel mills can significantly benefit from these upgrades, translating to higher productivity, reduced maintenance costs, and improved safety standards. Collaboration with specialized manufacturers ensures that the custom needs of each mill are met with precision and reliability.
List Quality Control and The Manufacturing Process of “steel mill crane”
Quality Control and Manufacturing Process of Steel Mill Crane
#### Manufacturing Process:
1. Design and Engineering:
– Initial concept and design based on client specifications.
– Detailed engineering drawings and structural analysis.
2. Material Selection:
– High-grade steel is chosen for strength and durability.
– Compliance with industry standards.
3. Cutting and Forming:
– Steel plates cut using CNC machines for precision.
– Forming processes like bending or rolling for structural components.
4. Welding and Fabrication:
– Components assembled and welded by certified welders.
– Non-destructive testing (NDT) on welds to ensure integrity.
5. Machining:
– Precision machining for mechanical parts such as gears and shafts.
– Surface finishing for corrosion resistance.
6. Assembly:
– Hoisting mechanism, electrical systems, and control units assembled.
– Integration of safety and operational features.
7. Testing:
– Rigorous operational and load testing.
– Functional verification and performance validation.
8. Surface Treatment:
– Application of anti-corrosion coatings.
– Finishing paint for aesthetics and protection.
9. Installation:
– On-site installation and alignment.
– Calibration and final testing.
#### Quality Control:
1. Incoming Material Inspection:
– Verification of material certificates and tests for composition and properties.
2. In-Process Inspection:
– Continuous monitoring during fabrication.
– Intermediate checks for alignment, dimensions, and weld quality.
3. Non-Destructive Testing (NDT):
– Ultrasonic, magnetic particle, or radiographic testing on welds.
– Ensures structural integrity without compromising the crane’s usability.
4. Load Testing:
– Testing at 125% of rated capacity.
– Ensures the crane can handle more than its specified load.
5. Final Inspection:
– Comprehensive review including functionality, safety systems, and performance.
– Inspection checklist adherence.
6. Documentation and Certification:
– Compilation of inspection reports, test certificates, and compliance documentation.
– Final certification by quality assurance team.
7. Client Acceptance Testing:
– Demonstration of crane operation to clients.
– Final adjustments based on feedback.
By integrating meticulous quality control throughout the manufacturing process, steel mill cranes are ensured to meet stringent safety and performance standards.
How to use “steel mill crane”
A steel mill crane is an essential piece of equipment used in steel mills for handling heavy materials like raw steel, steel coils, and finished products. Here’s a concise guide on how to effectively use a steel mill crane:
1. Pre-Operation Checks:
– Inspection: Examine the crane, hoist, cables, and hooks for any visible signs of wear, damage, or malfunction.
– Test Controls: Verify that all control buttons and levers are functioning correctly.
– Load Capacity: Ensure the load does not exceed the crane’s rated capacity.
2. Planning:
– Determine Path: Assess the route the crane will take and clear any obstacles.
– Communication: Establish signals or communication devices between the operator and ground personnel.
3. Operation:
– Load Attachment: Secure the load using appropriate slings or attachments. Double-check that it’s balanced and stable.
– Lifting: Gradually lift the load a few inches to ensure stability before fully raising it.
– Movement: Use smooth, controlled motions to move the load to the desired location, avoiding sudden starts or stops.
– Positioning: Carefully position the load at the destination. Lower it slowly to avoid impact damage.
4. Post-Operation:
– Unload Securely: Once the load is positioned, detach it carefully.
– Stow Crane: Move the crane to a designated resting position.
– Shut Down: Turn off controls and perform a quick post-operation inspection to identify any potential issues for maintenance.
5. Safety:
– PPE: Ensure all personnel are wearing appropriate Personal Protective Equipment (PPE).
– Awareness: Maintain vigilance about the surroundings and keep unauthorized personnel out of the operational area.
Using a steel mill crane involves methodical planning, adherence to safety protocols, and careful execution to ensure efficient and safe material handling in the steel mill environment.
“steel mill crane” Comparative Analysis
Comparative Analysis: Steel Mill Cranes
Steel mill cranes, pivotal in handling heavy materials, come in various forms, such as overhead cranes and gantry cranes, each with distinct advantages suitable for different mill environments.
Overhead Cranes:
Overhead cranes, also known as bridge cranes, are prevalent in steel mills due to their ability to cover extensive working areas. They operate on two parallel runways with a traveling bridge spanning the gap. These cranes can handle substantial loads, often exceeding 20 tons, and are ideal for environments requiring precise load distribution and high-frequency use. Their design facilitates heavy-lifting operations over long distances, making them essential for transferring molten steel, positioning large steel plates, and loading finished products. Modern overhead cranes are often equipped with advanced control systems, enhancing safety and operational efficiency.
Gantry Cranes:
Gantry cranes, similar in function to overhead cranes, differ primarily in their support structure. They are supported by freestanding legs moving on wheels or along a track, eliminating the need for permanent runway structures. Gantry cranes are versatile and can be employed within or outside the steel mills. Their mobility makes them suitable for tasks spanning different sections of a mill or even different sites. They are particularly advantageous in scenarios where rooftop support for an overhead crane is impractical or where space constraints necessitate flexible lifting solutions.
Comparison:
1. Structural Requirements:
– Overhead Cranes: Require robust building infrastructure for runway systems.
– Gantry Cranes: Need ground space for tracks or wheels but not fixed runways.
2. Mobility:
– Overhead Cranes: Limited to fixed tracks, providing less mobility.
– Gantry Cranes: Greater flexibility, can move across different areas and surfaces.
3. Load Capacity and Range:
– Overhead Cranes: Generally support higher loads, ideal for heavy and continuous lifting.
– Gantry Cranes: Versatile and adjustable but might offer relatively lower load capacities compared to heavy-duty overhead cranes.
4. Installation and Costs:
– Overhead Cranes: Higher initial setup costs due to structural modifications.
– Gantry Cranes: Potentially lower setup costs with easier installation but longer-term maintenance considerations.
In conclusion, the choice between an overhead and a gantry crane depends on the specific operational needs, structural conditions, and required mobility within the steel mill. Each offers unique benefits to enhance productivity and safety in demanding industrial environments.
“steel mill crane” Warranty and Support
Warranty and Support for Steel Mill Crane
At [Your Company Name], we understand the critical role that steel mill cranes play in your operations. That’s why we offer robust warranty and support services to ensure your equipment performs reliably and efficiently.
Warranty Coverage:
Our steel mill cranes come with a comprehensive warranty that typically covers a period of 12 months from the date of installation or 18 months from the date of shipment, whichever comes first. The warranty covers:
1. Manufacturing Defects: Any defects in materials or workmanship will be repaired or replaced at no cost.
2. Parts and Components: Essential parts and components, including motors, hoists, and hydraulics, are covered under our warranty.
3. Service and Labor: Costs related to the repair or replacement of defective parts, including labor, are covered under our warranty terms.
Exclusions:
The warranty does not cover damages resulting from:
– Improper installation or maintenance not performed by certified technicians.
– Modifications or repairs not authorized by [Your Company Name].
– Abuse, misuse, or neglect.
– Natural disasters and other force majeure events.
Support Services:
To ensure continuous operation and minimize downtime, we offer the following support services:
1. 24/7 Customer Support: Our dedicated support team is available around the clock to address any emergency issues.
2. Scheduled Maintenance: We provide regular maintenance routines to keep your crane in optimal condition, reducing the likelihood of unexpected breakdowns.
3. Spare Parts Availability: We maintain a comprehensive inventory of spare parts to ensure quick replacements whenever necessary.
4. On-Site Assistance: Expert technicians can be dispatched to your location for on-site assessments, repairs, and preventive maintenance.
5. Training Programs: We offer customized training programs for your staff to ensure they are well-versed in operating and maintaining the crane safely and efficiently.
For detailed terms and conditions of our warranty and support services, please refer to your purchase agreement or contact our customer service department. We’re here to support your operations and ensure your investment delivers high performance and reliability for years to come.
—
[Your Company Name] Customer SupportPhone: [Customer Support Number]
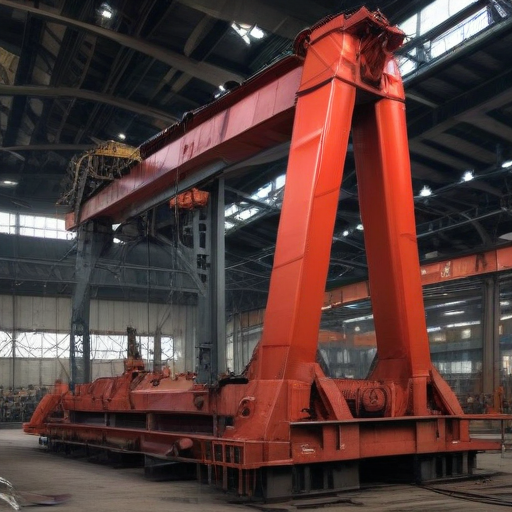
List “steel mill crane” FAQ
Steel Mill Crane FAQ
Q1: What is a steel mill crane?
A steel mill crane is specialized equipment designed to handle, move, and load heavy steel products in steel mills. These include overhead cranes, gantry cranes, and jib cranes, among others.
Q2: What types of cranes are used in steel mills?
Common types of cranes in steel mills are overhead (bridge) cranes, gantry cranes, and ladle cranes. Each type serves different functions, from transporting molten metal to moving finished steel products.
Q3: What capacities do steel mill cranes typically have?
Capacities range widely, from a few tons for smaller operations to over 500 tons for large, industrial-grade cranes, depending on the specific needs of the mill.
Q4: How are steel mill cranes operated?
Most cranes are operated using a cabin with joysticks and controls, although some modern cranes may also be operated via remote control systems.
Q5: What safety features are included in steel mill cranes?
Key safety features include limit switches, overload protection, emergency stop buttons, anti-collision systems, and thermal protection for motors.
Q6: What maintenance is required for steel mill cranes?
Regular maintenance includes inspecting and lubricating mechanical components, electrical system checks, and replacing worn-out parts. Regularly scheduled maintenance is crucial for safe and efficient operation.
Q7: Can steel mill cranes be customized?
Yes, these cranes can be custom-designed to meet the specific needs and spatial constraints of a particular steel mill.
Q8: How do steel mill cranes handle extreme temperatures?
Crane parts are often made of materials that can withstand high temperatures, and some come with additional insulation or cooling systems to protect the machinery and operator.
Q9: Are there any environmental concerns associated with steel mill cranes?
Yes, cranes can emit noise and sometimes have issues with oil leaks, which need to be managed to reduce environmental impact.
Q10: How do steel mill cranes improve productivity?
They enhance efficiency by significantly reducing manual labor and time required to move heavy and bulky materials, thereby speeding up production processes.
Top 10 FAQ with answer about steel mill crane for Buyer Sourcing from China
Sure! Here are the top 10 frequently asked questions (FAQ) about sourcing a steel mill crane from China, along with concise answers:
1. What types of steel mill cranes can I source from China?
– China manufactures various types of steel mill cranes, including overhead cranes, gantry cranes, jib cranes, and electric hoists. These cranes come in different capacities and configurations suitable for steel mill applications.
2. How do I ensure the quality of the crane?
– Verify certifications like ISO, CE, and CCC. Request detailed technical specifications, past project references, and conduct factory audits if possible. Use third-party inspection services to assess quality pre-shipment.
3. What is the typical lead time for a steel mill crane from China?
– The lead time generally ranges from 8 to 16 weeks, depending on the complexity and customization required. Communicate clearly with suppliers about your timeline needs.
4. Is customization available for specific requirements?
– Yes, most Chinese manufacturers offer customization options to meet specific operational requirements, including lifting capacity, span, and environmental factors.
5. What is the estimated cost, and how is it determined?
– Costs vary based on crane type, capacity, and customizations. Obtain detailed quotations and compare them. Consider factors like materials, design complexity, and additional features.
6. What about warranty and after-sales service?
– Most reliable manufacturers provide a 1-2 year warranty on major components. Ensure the supplier offers robust after-sales support, including spare parts availability and technical assistance.
7. How are logistics and shipping handled?
– Manufacturers typically manage the logistics, but you can also use your freight forwarder. Clarify if the price is FOB (Free On Board) or CIF (Cost, Insurance, Freight) and plan for port clearances.
8. What are the payment terms generally offered?
– Common terms include a 30% deposit before production and 70% balance before shipment. L/C (Letter of Credit) and T/T (Telegraphic Transfer) are widely accepted.
9. How do I address language and communication barriers?
– Work with suppliers proficient in English. Use clear and concise language, confirming all technical details and agreements in writing.
10. Are there any import duties or taxes I should be aware of?
– Import duties and taxes depend on your country’s regulations. Consult with customs brokers to get accurate information on the applicable import duties and ensure compliance.